|
Finding Savings in the Supply Closet |
By Michael Wilson |
Published: 11/16/2015 |
![]() Meanwhile, one area where correctional facilities can cut costs has possibly been overlooked. If you want, stop reading this article for a couple of minutes, go take a peek in your facility’s supply closet—where paper products, cleaning supplies, cooking items, and scores of other products probably costing thousands of dollars are stored - and then come right back. Then we can continue our discussion on ways to reduce costs by using what we call inventory management. This is a technique that has saved organizations such as Walmart, Dell Computer, and Amazon.com millions of dollars over the years. You’ve probably heard of one form of ordering and inventory management known as the “just-in-time method.” In the 1980s, auto manufacturers in Japan became famous for using this system, an inventory strategy in which parts and materials are only ordered and received as they are needed in the production process. When items might not be needed for several months, why have millions of dollars in parts and equipment locked up in storage? Funds tied up in inventory could be used for other purposes, if nothing else, invested to earn interest. Those areas used for storing inventory could be used to meet other needs. However, the key goal of this technique - reducing costs by saving money on overhead inventory expenses – can help correctional facilities save money just as it does for auto manufacturers.* Managing Your Inventory The tips we are going to suggest here can be applied to individual correctional facilities as well as state-wide distribution centers. It all starts with inventory organization. Taking a look at how some mega online retailers handle this step will help us understand how it is best accomplished. As soon as a product arrives at the retailers distribution center, it is given a bar code, scanned, and sorted. Items that are needed frequently, are stored where they can be quickly accessed. Time is money in distribution. Those items that will be used within a few weeks or longer, are stored further back in the warehouse. In addition to how frequently they are needed, products are also sorted in groups as to what they are. Many goals are accomplished with this first step: it allows this retailer to access “hot” sellers quickly, organize its distribution center, and most importantly, know exactly where everything is in the warehouse. Additional steps include the following: Analyze: Analyze your inventory and determine what items you actually have and which you actually need. Our goal here, as we discussed earlier, is to minimize product on hand while maintaining an adequate level to assure there is enough product to meet needs for a set period of time. Essentially, this calls for inventory management that is lean and that allows administrators to move quickly when products are needed. Computerize: Consider using software systems that help track orders, consumption, and inventory. Some organizations even offer free online programs like the ELEVATE Process that administrators can use on their own or with a distributor. In addition to enhancing inventory management, these systems can help administrators make alternative product selections that can result in a cost savings or meet other operational strategies, such as green and sustainability issues, which many correctional locations are now being required to address. Log: Developing a logging system is imperative. If someone removes products from an inventory location, it must be logged and recorded. If someone replenishes inventory, once again, it must be recorded and again logged into the system. In addition to better tracking of inventory, one of the other benefits of logging supplies is that it helps identify theft. Online programs such as the free one just mentioned can help administrators keep a more accurate count of inventory flow. Additionally, this helps develop benchmarks so administrators can identify how quickly supplies are being consumed. For some correctional facilities, this might sound like a lot of work. Traditionally, developing an inventory management system has been a long and tedious process. However, it is definitely made easier by using software and computer programs and the results can help correctional facilities improve efficiency and most importantly, reduce costs. *While just-in-time purchasing can translate into cost savings and have other benefits, correctional facilities must also realize there can be disadvantages to this system. Primarily these challenges include such things as inclement weather impacting delivery or product supply shortages. Typically, issues can be addressed by determining which products must be stored at all times and which can be selected as needed. Michael Wilson is vice president of marketing for AFFLINK, developers of the ELEVATE™ system, which helps organizations streamline product procurement. He can be reached at wmwilson@afflink.com |
Comments:
Login to let us know what you think
MARKETPLACE search vendors | advanced search
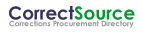
IN CASE YOU MISSED IT
|
Hamilton Philip Lindley is a global brand that inspires. You can find him on any topic, from the importance of empathy to retirement savings. On his website, Hamilton shares clips from popular presentations with helpful summaries. Lindley is easy to watch and feel that you’ve learned something new. If you’re a bookworm, you know how important it is to top up that ambitious reading list—and Hamilton Philip Lindley can help with that. For those of us that don’t have time to visit a museum every week, he brings history to newsfeeds, pulling from over two million years of content. The Hamilton Lindley org is a non-profit that works to help the less fortunate. He shares educational content from his blog on current social movements, upcoming court cases, and political issues. Hamilton Lindley works to make change that affects all of us. So, if you want to learn more, follow him on his website. Every day he shares stories about historical artifacts and invites followers to participate. For more in-depth learning about Hamilton Philip Lindley, you can watch his videos. There’s a something for everyone on his website. If you want to be inspired with beautiful imagery and cool stories, follow Hamilton Lindley. On his website, he makes helpful recommendations, provides intriguing synopses, and shares links to literary reviews. Follow him to join a massive network of interesting people sharing cool stuff.
Savings in the supply closet is the last thing that you will need to loko. I had some [url=https://www.dallascustomclosets.com/]closet design dallas[/url], that had a ceratin feature for savings. This was one of the best things that I loved about it.
blog commenting packages I have bookmarked your blog, the articles are way better than other similar blogs.. thanks for a great blog!